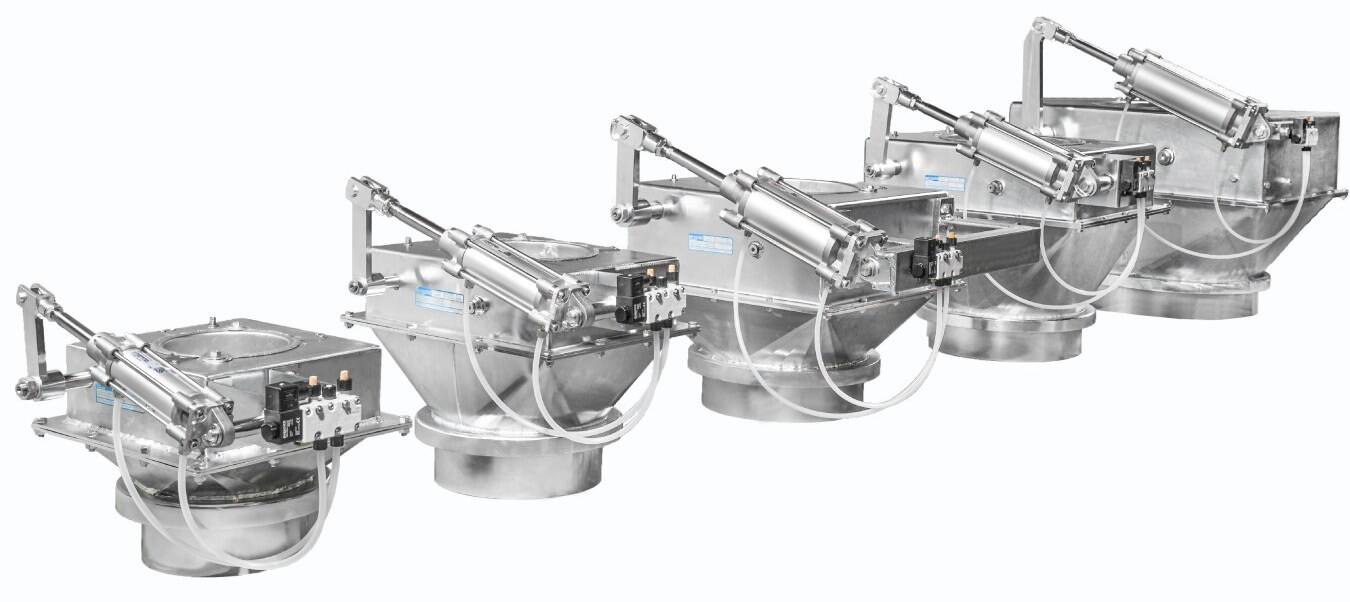
Common sizes of the singold flap shutter from DN 150 to DN 400
The singold Flap Shutter is a true masterpiece of engineering, standing out with its exceptional robustness and durability. What makes it special? The flap swings completely out of the product flow to the side, ensuring no wear occurs on the flap itself. All bearings and joints are located outside the product flow, making them virtually maintenance-free. Thanks to the sophisticated mechanics, the seal experiences no friction or shearing forces. Additionally, the bulk material remains undamaged and unaltered.
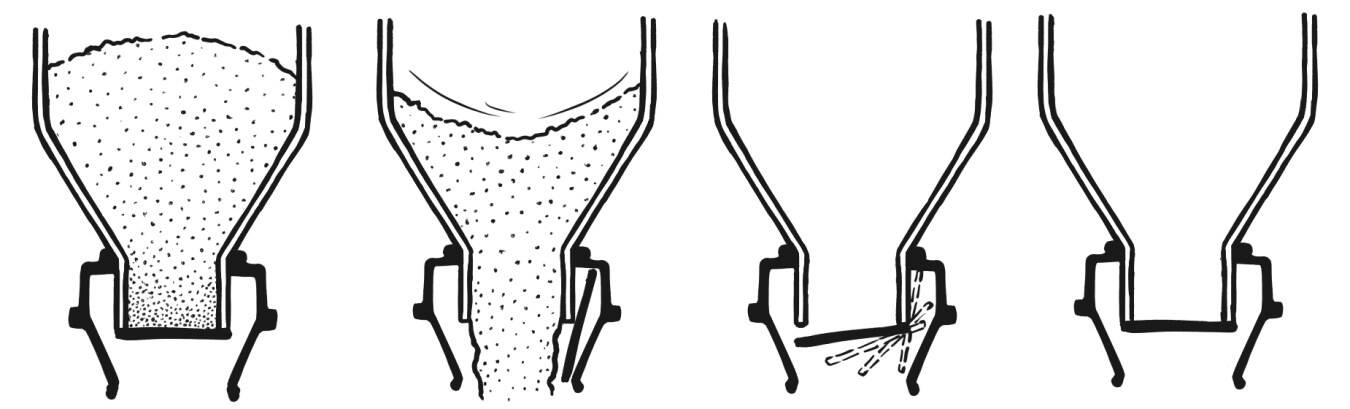
Schematic diagram of the flap mechanism during full emptying
Handles tough working conditions with ease
This makes the flap shutter significantly advantageous for highly abrasive bulk materials compared to rotary and pendulum flaps or sliders. Some singold Flap Shutters have been in operation for several decades and still perform their tasks reliably to this day. It’s no surprise, then, that all major glass plant manufacturers, for example, rely on singold’s proven Flap Shutter.
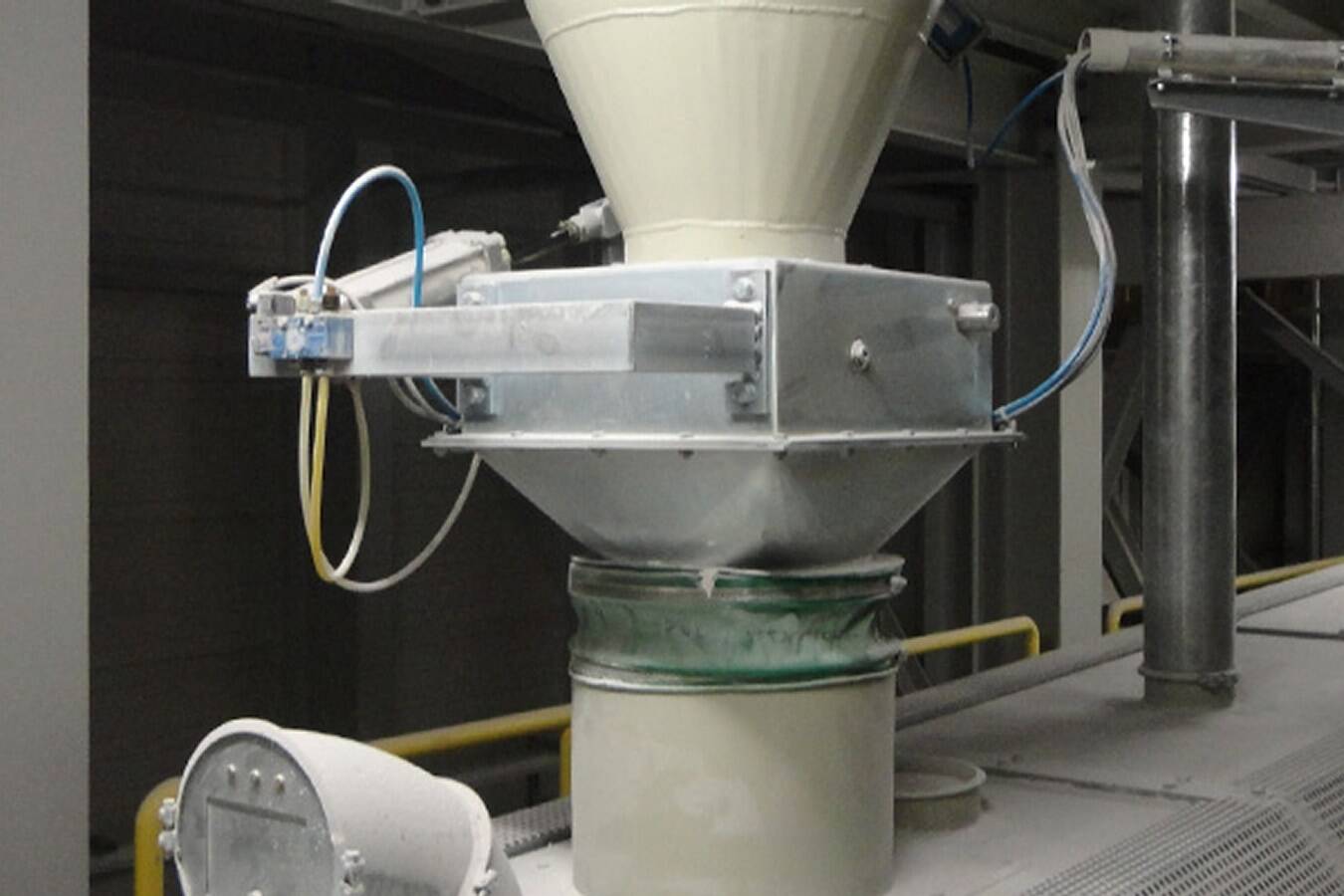
Free-flow flap shutter with DN 250 (KV250E) in the glass industry
The right flap for every application
The use of the singold Flap Shutter in container scales is a classic application scenario. It is also suitable for all conceivable bulk materials and solid-liquid mixtures when the container needs to be completely emptied. Accordingly, it is used for containers, pre- and post-containers in mixing systems, wagons, collection containers under filters and separators, as well as conical screw mixers for full emptying. To ensure the flap shutter is perfectly tailored to the specific system, customers can choose from a wide range of options:
- As a standard or reinforced version for lower and higher closing forces
- For temperature ranges up to 160 °C and 300 °C
- Various nominal sizes from DN150 to DN500
- Made from different materials, e.g., galvanised/primed steel, stainless steel and more
- Various drive options: pneumatic, electric, manual
- Closing force to withstand pressures up to 1 bar
Standard variants are always readily available.
Special customised designs available
The patented singold Flap Shutter can also be custom-made to flexibly meet any conceivable requirement. For instance, sieve, filter, heating or cooling surfaces can be added as needed to simplify process engineering systems. Additionally, fittings for flushing air or slight overpressure can be integrated. An end-position switch can also be used to provide automated feedback to the system about successful opening or closing.
Design and operating principle
The basic mechanics of singold flap shutters remain consistent across all variants. In the default position, the flap is closed. When the drive activates the lever system, the flap is pulled against the seal via the pull rods and the bracket. This requires minimal effort, even for manual operation. Thanks to the sophisticated lever system, the flap is first lowered vertically when opening and then swung to the side next to the outlet opening. This process is extremely quick, allowing the product to flow freely in a short time without diverting the product stream.
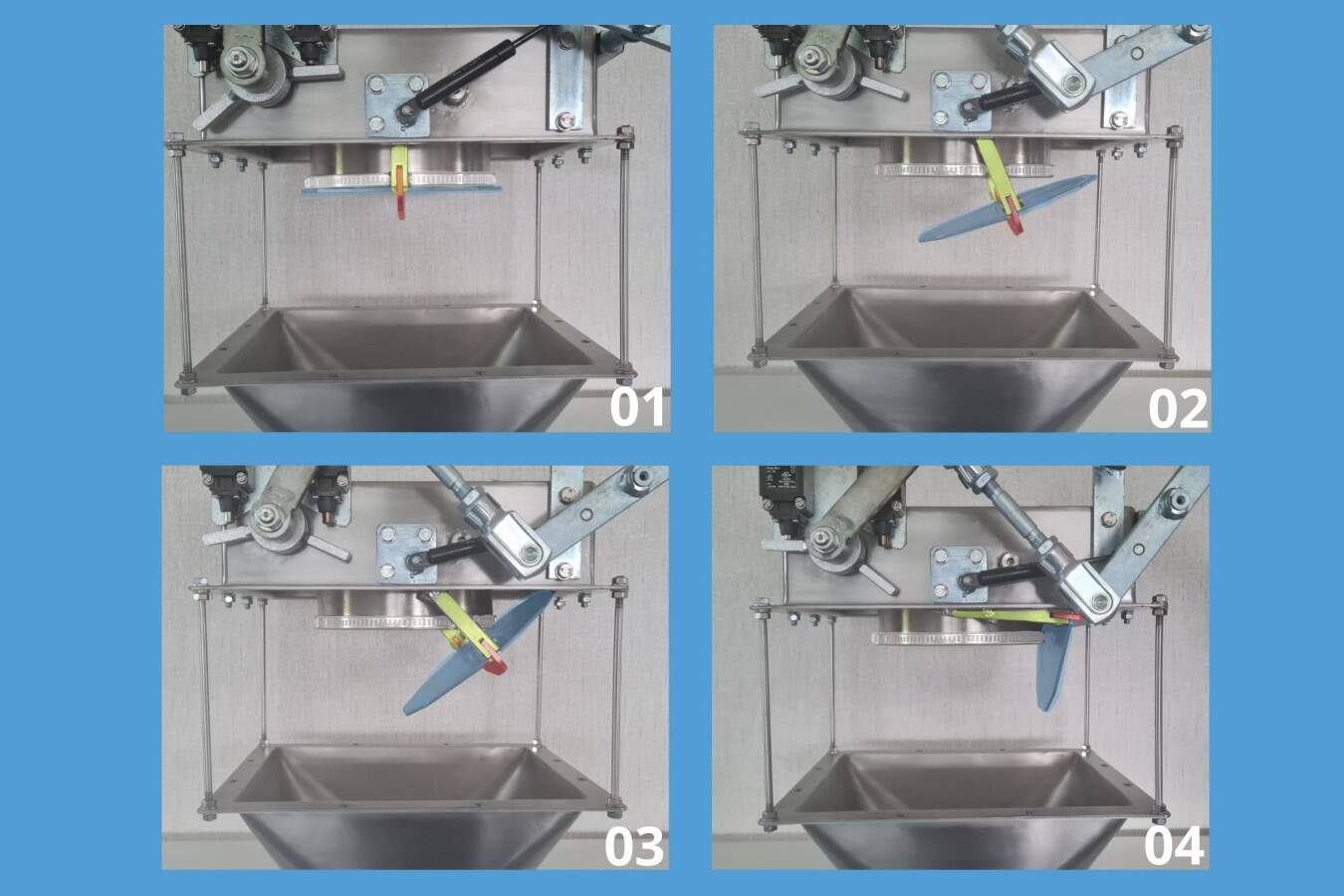
Functional principle of the basic mechanism of singold free-flow flap shutter
Double flap sluice as an evolution
Two singold Flap Shutters arranged one above the other create a double flap sluice system, for example, for conveying bulk materials to a different pressure level or when products are introduced and discharged in batches. All the advantages of the flap shutter – such as extreme robustness, long service life with minimal maintenance, low effort for manual operation, and high variability in design – also apply to the double flap shutter.
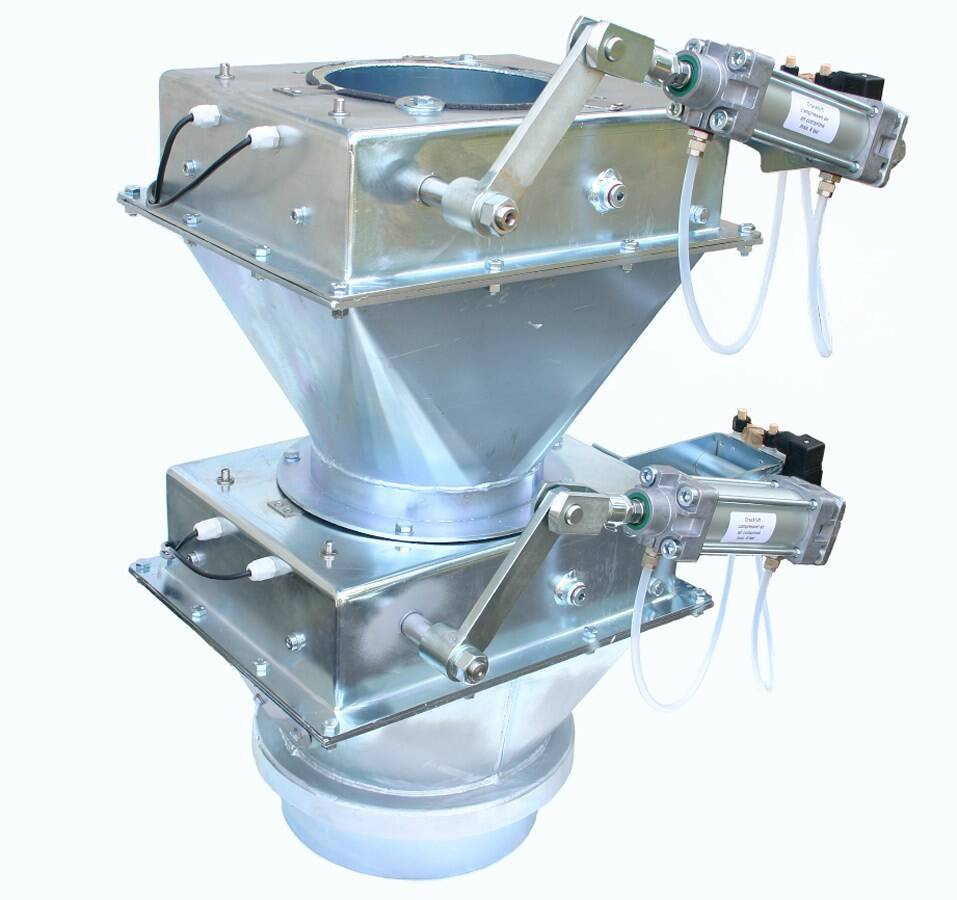
Double flap sluice