The drying of materials is often the prerequisite for their further processing. The drying process, i.e. the thermal removal of water and other liquids, makes the dried goods durable, mixable, grindable or otherwise usable for further process steps.
Drying processes have been industrial standard for many decades already. The first belt dryer in Europe, for example, went into operation as long ago as 1907. These days, belt dryers are used in a wide range of different branches. Examples include belt dryers for timber, pharmaceuticals, food, plastics, wastewater sludge and many other organic substances. All these substances have one thing in common: they are combustible and, in combination with a belt dryer, result in a high fire load.
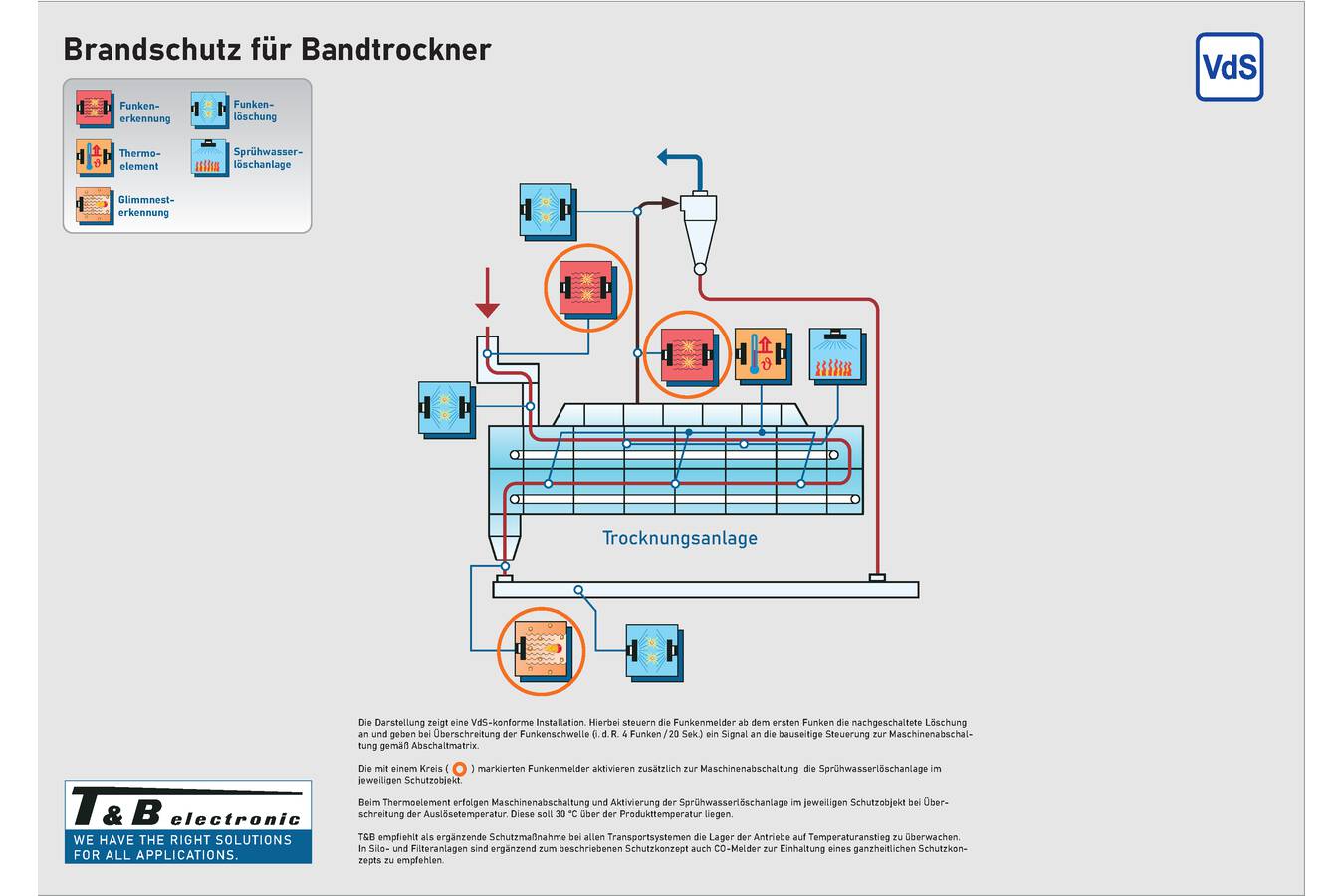
New VdS-certified fire protection concept for belt dryers
The importance of belt dryers in industrial applications has increased significantly over the past few years. Generally, standard series belt dryers have a modular design. They are made up of a product feeding module, a drying module and a discharge module.
The task of the product feeding module is to feed the supplied material continually and evenly onto the belt within the dryer. The actual drying of the material takes place in the drying module by supplying preheated air which absorbs the moisture of the material to be dried and removes it from the system via extraction or exhaust air lines. Dwell times of up to 30 minutes are quite common, depending on the length of the dryer belt and the material properties. At the end of the drying module, the product often has a residual humidity of only 3%. The discharge module transfers the material to the downstream conveyor without damaging the structure of the dried material.
The drying process via belt dryers has several advantages over other drying processes, which is why the number of belt dryers has risen sharply in recent years. However, the increase in numbers of belt dryers has also led to an increase in fire incidents, which has drawn the attention of leading insurance companies to the often poor fire protection for belt dryers. HDI has, among other things, presented a concept for extinguishing fires in belt dryers in one of its numerous fire protection guides. On this basis, T&B has now created a certified protection concept in cooperation with VdS.
Fire protection in belt dryers
Why is fire protection in belt dryers important and is a VdS-certified protection concept necessary? Numerous fire incidents in the past have shown that fully comprehensive fire protection in belt dryers is elementary. Due to various unfavourable factors, the fire risk in belt dryers is increasing dramatically. On the one hand, we have the relatively high drying temperatures, increasing dryness of the material and high dust content. On the other hand, the high proportion of material in such plants should not be underestimated, which is why the fire load must be considered very high. If sparks enter the belt dryer during the process e.g. through upstream processes, or if hot layers of material which are created by deposits in the dryer, lead to pockets of embers, a very rapid spread of fire is to be expected.
In the past, there have been various approaches to representing fire protection in a belt dryer. For example, sprinkler systems were used to protect belt dryers. A sprinkler system is only suitable to a limited extent for the protection of enclosed objects, because in the event of a fire in the dryer, the sprinkler is triggered and extinguishes the fire locally. However, the adjacent sprinklers are cooled by the water mist so that they are no longer triggered, even though the fire has most likely already spread. A spreading of the fire, so-called “sprinkler skipping” is thus very probable.
Water spray extinguishing systems are an alternative here. Unlike sprinkler systems, water spray extinguishing systems have an open nozzle network and can wet the dryer with a fine water spray pattern over the entire area when triggered. Activation can be pneumatic via thermal trigger elements or electrical e.g. via heat detectors or flame detectors.
When water spray extinguishing systems are used, however, there are uncontrollable general conditions that can lead to a fire despite the installation of the extinguishing system. On the one hand, sparking caused by upstream processes cannot be prevented and, on the other hand, pockets of embers in the discharge area cannot be detected at an early stage, which could result in a rapid spread of fire inside the belt dryer and fire spreading to downstream areas.
For the sake of completeness, the sluggish triggering behaviour of the thermal trigger elements should be mentioned here as a significant disadvantage. Thermal trigger elements and heat detection do make sense in the case of standstill monitoring, but are not the optimum solution when the process involves movement, since a temperature increase due to smouldering fire is very difficult to detect due to the permanent air exchange.
The critical general conditions mentioned and the disadvantages of thermal trigger elements are an argument in favour of installing a spark extinguishing system. By installing highly sensitive IR spark detectors in the input module, sparks can be detected at an early stage and extinguished selectively, preventing potential ignition from upstream processes from entering the drying process in the first place. In addition, IR spark detectors can also be implemented in the exhaust air ducts of the belt dryer. The high exhaust air temperature is prevented by means of fibre optics, which means that the spark detectors can be used without any reservations even in this harsh environmental condition. This way, the smallest sparks and hot particles which occur e.g. in smouldering fires can be detected as early as possible.
To prevent fire spreading to downstream plant areas, so-called combination detectors are installed in the output module. These detectors combine the properties of conventional spark detectors and ember detectors and are thus able to detect both sparks and pockets of embers. In case of detection, automatic extinguishing systems are also activated in the output module, which extinguish the affected material selectively. The special feature here is that automatic extinguishing systems are activated both below the detectors in the direction in which the material falls and above the detectors in the direction of the dryer belt. Since belt dryers are operated under negative pressure, the installation of the automatic extinguishing systems above the detectors has proven its worth in practice. Without these automatic extinguishing systems, it is very likely that sparks or hot particles will be sucked back towards the belt by the negative pressure in the belt dryer and can have devastating consequences.
However, neither the conventional water spray extinguishing system nor the classic spark extinguishing system provide fully comprehensive fire protection for belt dryers.
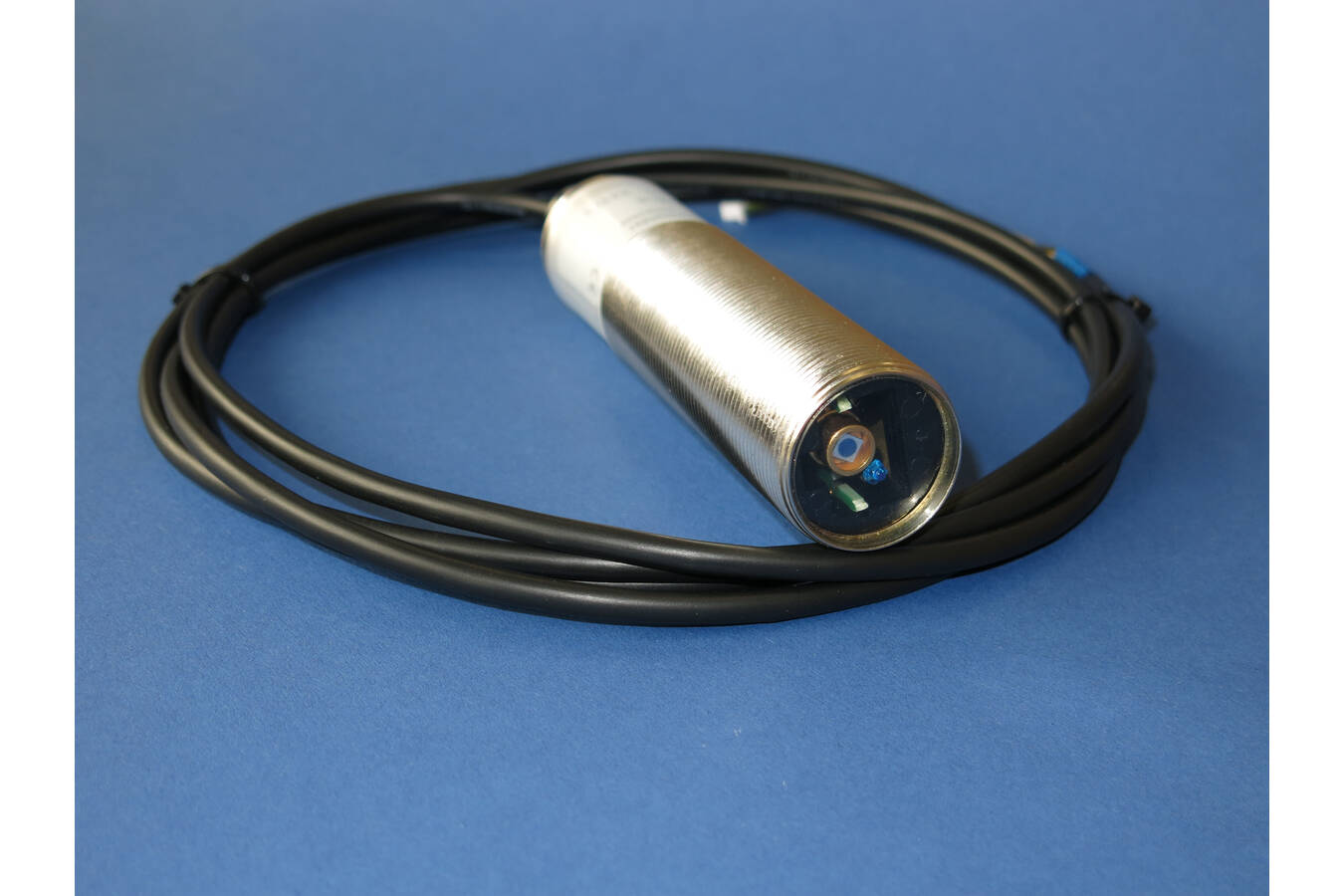
New T&B combined detector of the type FSM for the detection of both sparks and embers
Both systems combined
What is the conclusion? Correct, the two fire protection systems are combined. T&B has used the advantages of both systems and combined them together with VdS in a new type of protection concept. The water spray extinguishing system provides comprehensive fire protection within the belt dryer and the spark extinguishing system is used for preventive fire protection and the earliest possible activation of the extinguishing system.
For this purpose, a special activation concept was developed which enables the spray extinguishing system to be triggered via the spark detectors or combination detectors in the input and output module as well as the spark detectors in the extraction lines. This enables the fastest possible triggering of the water spray extinguishing system and minimises damage to the belt dryer, thus reducing costly machine downtimes.
The VdS certification of this fire protection concept has now created a uniform standard that guarantees the greatest possible safety and machine availability and is also accepted by every property insurer. Time-consuming coordination and uncertainties about the acceptance of the fire protection implemented for belt dryers are now a thing of the past.